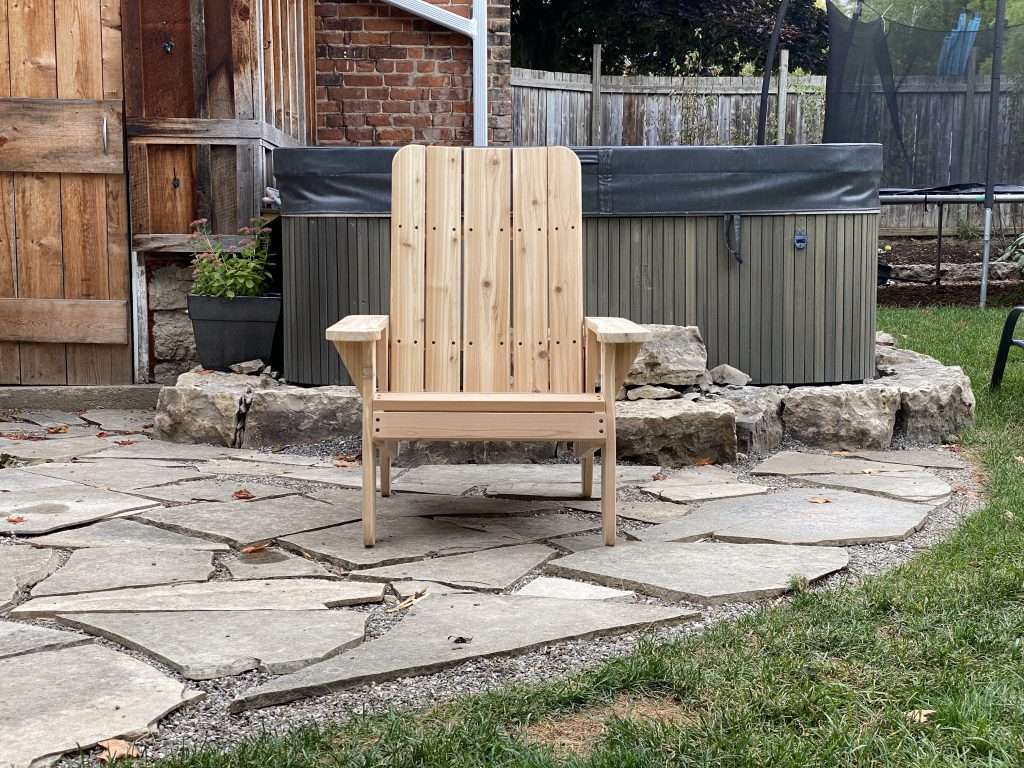
Hey folks. I’m excited to share a new project and all of the files and details to make an Adirondack/Muskoka chair on the LongMill! Scott, our in-house content creator and maker-supreme, wanted to add a few nice, high-quality chairs for his backyard, and so we set out to make a CNCable chair that can be made on the LongMill and basically any hobby CNC of a similar size.
This project was designed by me (Andy) and cut out by Scott in his shop. While this project has a lot of parts, the actual process to make them should be pretty straightforward since a lot of it is repetitive setup and cutting. While this is a perfect project for a beginner, I encourage advanced users to find ways to customize and modify our designs to add their own unique flair.
We continue our series of projects that you can make with your LongMill. To check out the one from before, visit our page here: https://sienci.com/2022/08/04/how-to-make-a-giant-connect-4-on-your-longmill. You can support us by subscribing to our Youtube channel and sharing projects that you’ve made from our designs online! If you have any ideas or projects you want to see us do, feel free to reach out or comment on our social media!
You can find all of the gcode files here: https://drive.google.com/drive/folders/1HEG-XiYE3hG1Z1tJLN5Ur_43JNt-_sXb?usp=sharing
You can find the original Onshape Document here (the recommended version is V4.5): https://cad.onshape.com/documents/0b19b5ee496fd69e78919e94/w/a8b4c856489564350c8ada96/e/4abebe412558dcc22732668c?explodedView=Ml0pbn89RON32w9a4&renderMode=0&rightPanel=explodedViewPanel&uiState=633dac6ace61db730030fc6b
The design process
This was a bear to design. There were a lot of things we learned through the 4 or 5 different iterations it took to hammer it out. During the design process, it’s important for us to not just make a great design, but make it so that:
- The materials you need for the project can be found universally and at a reasonable price
- The materials can be of varying qualities but still work
- The design can fit on a standard 30×30 working area
- The tooling and techniques to make the project is accessible and easy enough for beginner users
Here’s what some back and forth looked like between me and Scott for making updates:
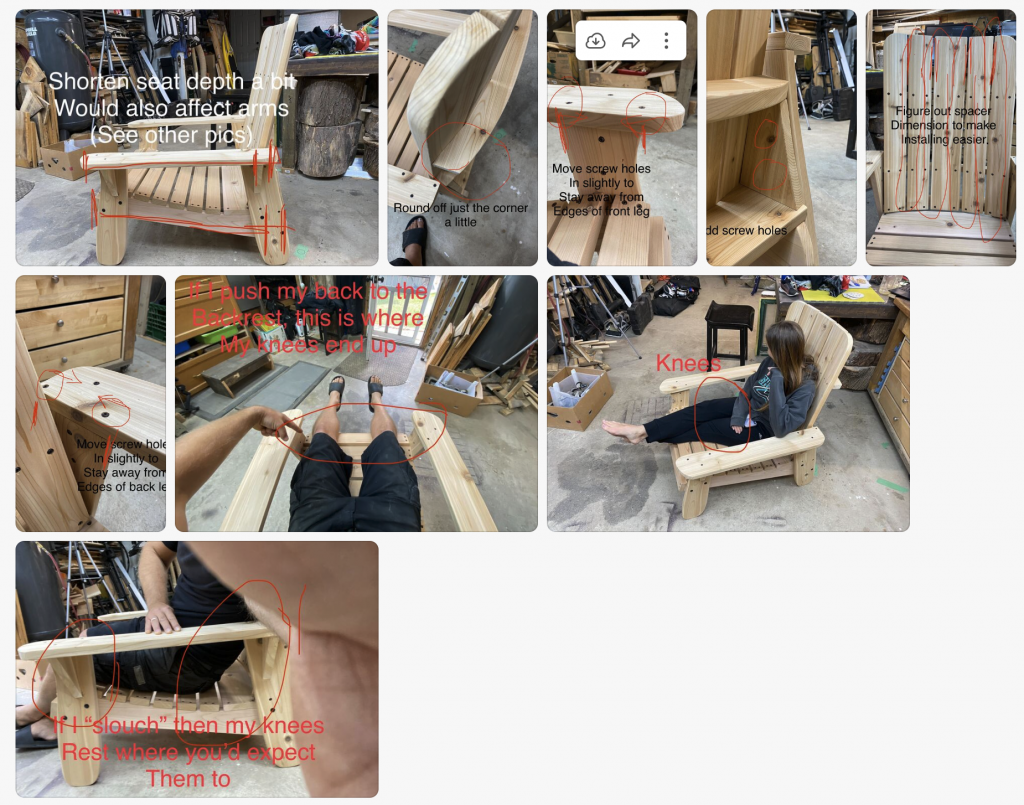
The newest version has some tweaks made compared to the version in the video which include:
- Better placement of screw holes
- Slightly shorter chair to fit knees better
If you see a design flaw, please feel free to let us know.
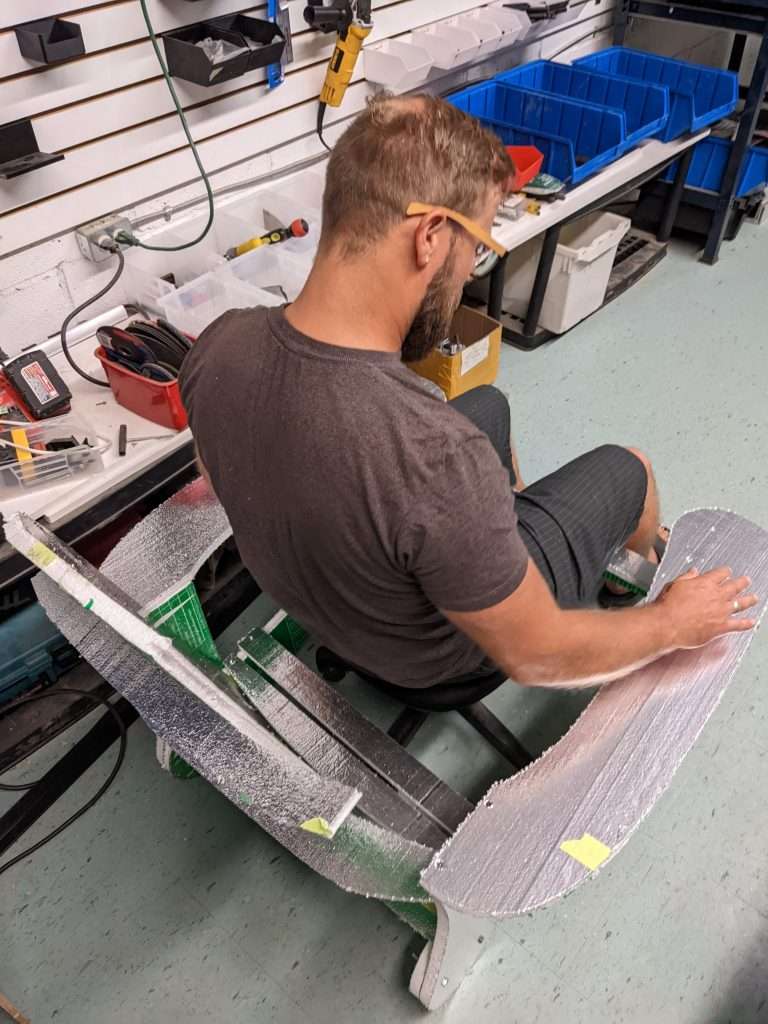
Finding the right materials
Finding the right materials for this project was a major challenge. Our first prototype used some 3/4″ cedar boards, but because lumber manufacturers are bad at measuring things, the actual thickness came out closer to 1/2″, but not to a degree of consistency that would let us make good joints without doing extra work planing and cutting down the boards. There was a lot of warp and cupping in the boards, making it even more difficult to fit things together. This resulted in poorly fitting parts and weak spots in the cut boards.
You can probably see it better in these photos and videos below:
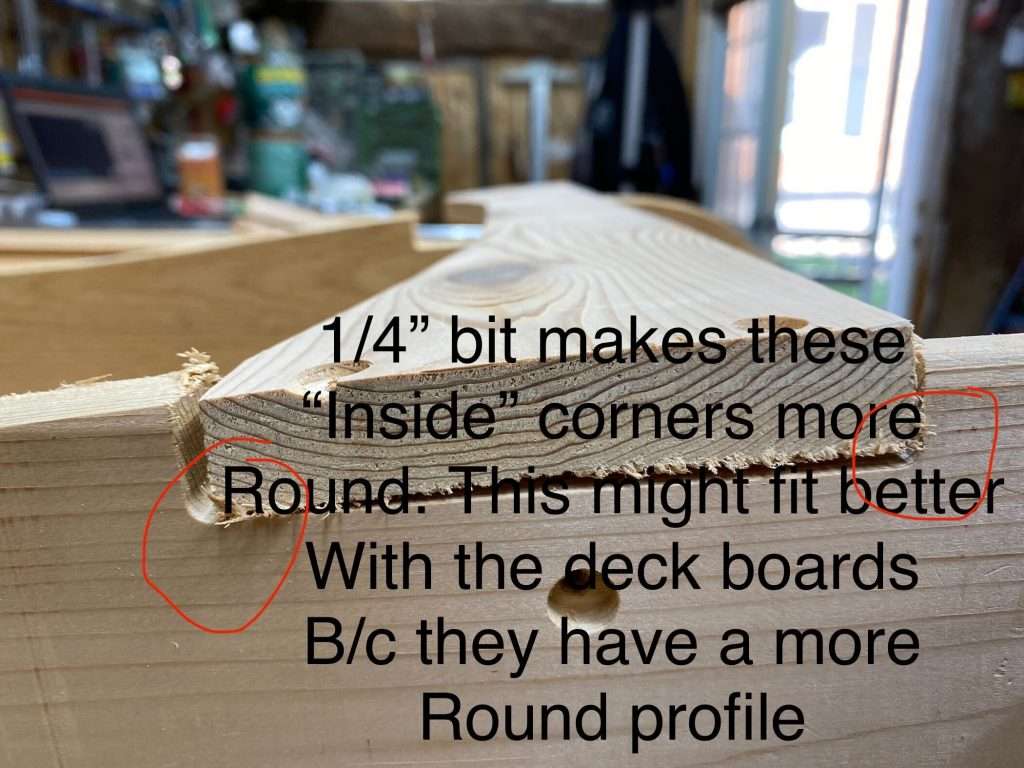

The material we finally settled on, deck board, was much stronger, flatter, and thicker. Although its a bit overkill for making a chair, using the higher quality material makes it easier overall to work with. Here’s a link to the material that we used: https://www.homedepot.ca/product/porcupine-5-4x6x8-premium-knotty-cedar-decking/1000167641
3/4″ wood is strong enough for this project, so if you can get it while being dimensionally stable, I would probably get that stuff. The Onshape document does have some variables to help you adjust the size of the model based on the material thickness.
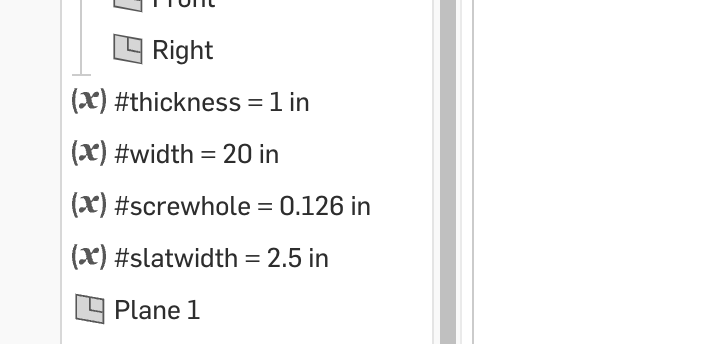
Another slightly annoying constraint was the widths of the wood we could buy for this project. It was important to us to use solid wood, at least for the sake of the asthetics that Scott wanted for his house, so we needed to use standard size boards. In our case, the best option was to use 6in wide boards (or 5.5 – 5.7in roughly), all of the parts needed to fit within that width.
According to Scott, this project uses about 56 feet of board (or 7 x 8 ft boards).
Slotting and lining things up
If you’ve seen some of the other designs I’ve made, I like to have things slot and fit together. The Connect 4 would be a good example.
Well, given the variability of the thickness in the wood boards, even between throughout the board itself, it was hard to make a design that could actually have parts slot together. So I instead removed the need for things to slot together at all. This means that even if your material isn’t exactly the right thickness, you’ll still get a great chair. Basically all of the parts have a line or surface that can be used to line things up when putting the chair together (the arm support triangles are going to need a bit of eye-balling).
Cutting
Originally we had planned to cut the project using 1/4″ bit for the outside profiles and a 1/8″ bit for the holes, but we found that a 1/8″ bit for the whole project was a lot more convenient given that there’s no tool changes involved and less dust to clean up. Using the smaller bit does end up being a bit slower, but since this is a one-off project, time wasn’t a huge concern.
Cutting all of the parts should take about 2, maybe 3 hours. You can use feeds and speeds that you are comfortable with your material, but the gcode provided in the project files are set to 100IPM at 0.2″ depth of cut. It’s likely you can bump up the speed while cutting to your taste with the manual feedrate overrides.
Workholding
Scott suggests using hot glue as a way to keep the part coming out of its spot while cutting. I think this is a pretty good method overall, albiet a bit messy at times. For myself on the otherhand, I will cut the screw holes first and use them as a place to put some wood screws to keep the part in place as the outside gets cut out. Either method works.
Assembly
Please enjoy these exploded views of the chair. You can also check our 3D model as a reference for where things should go.
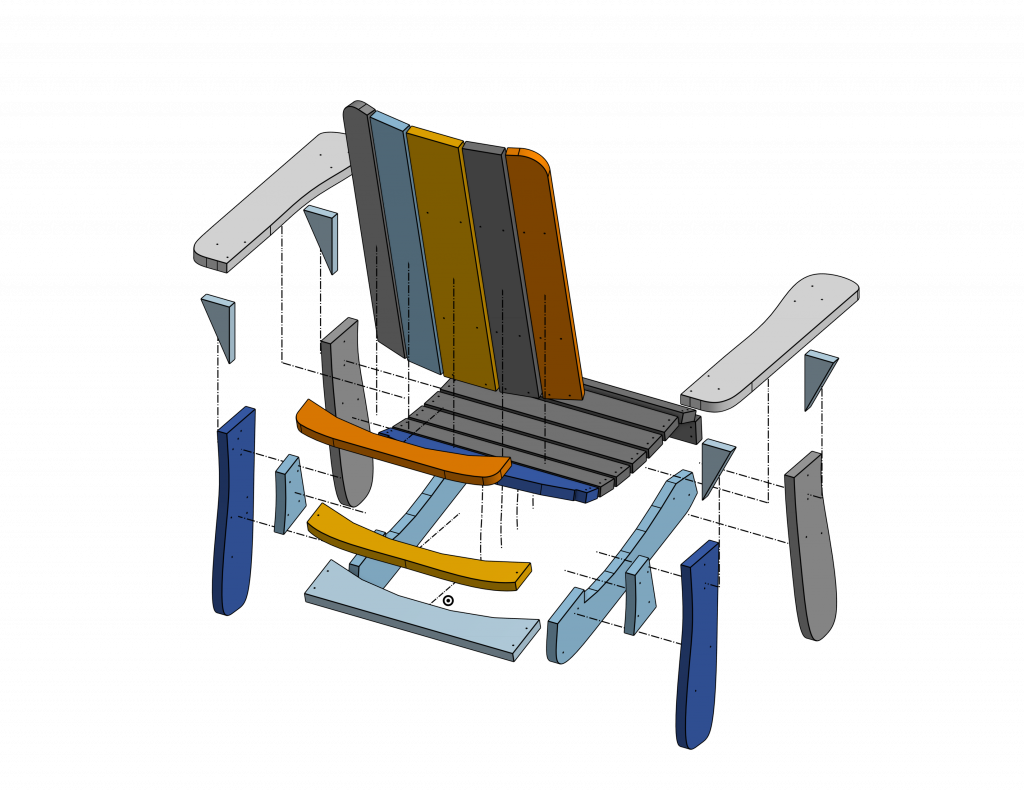
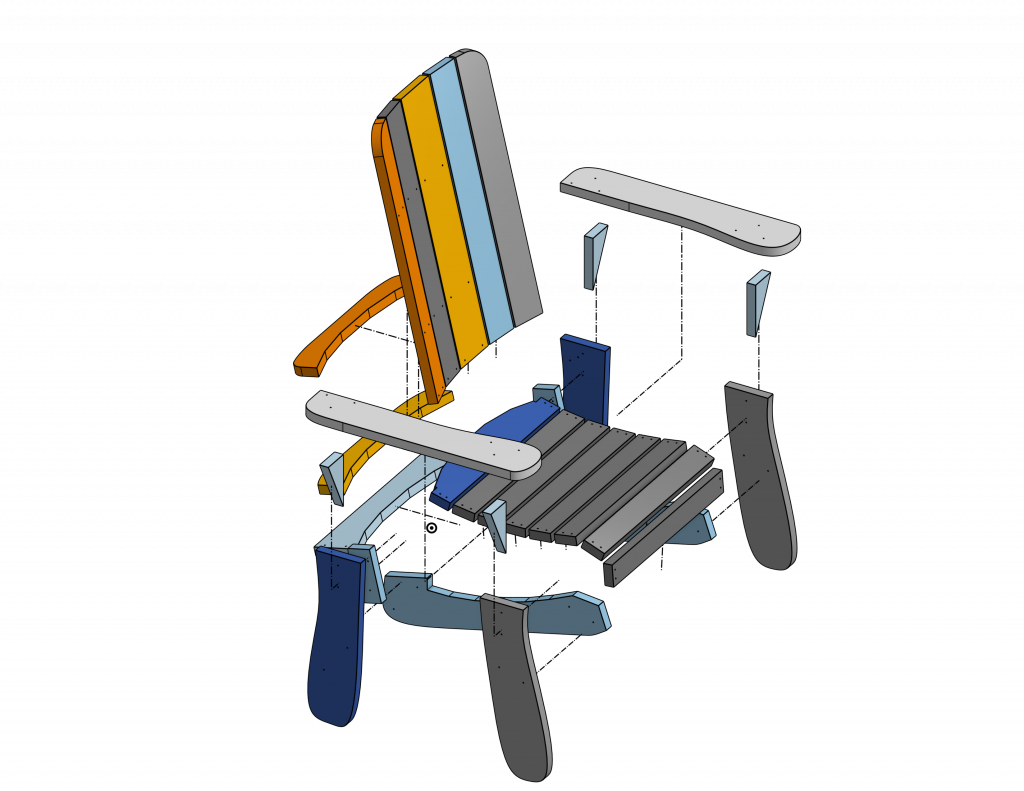
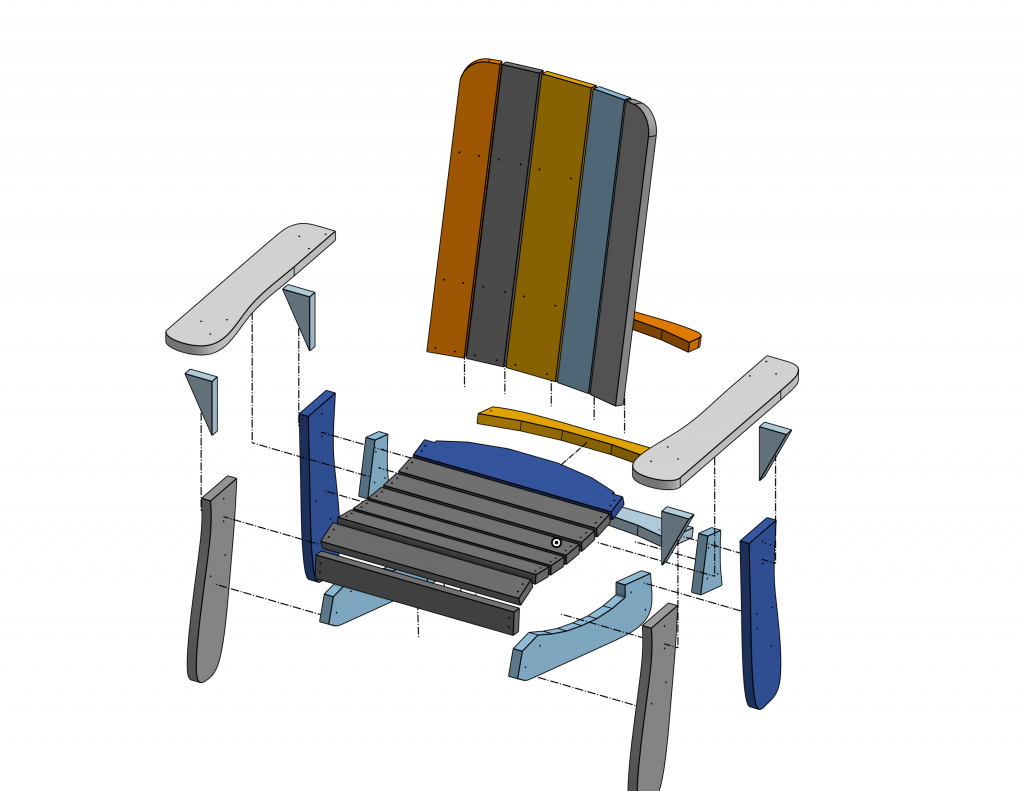
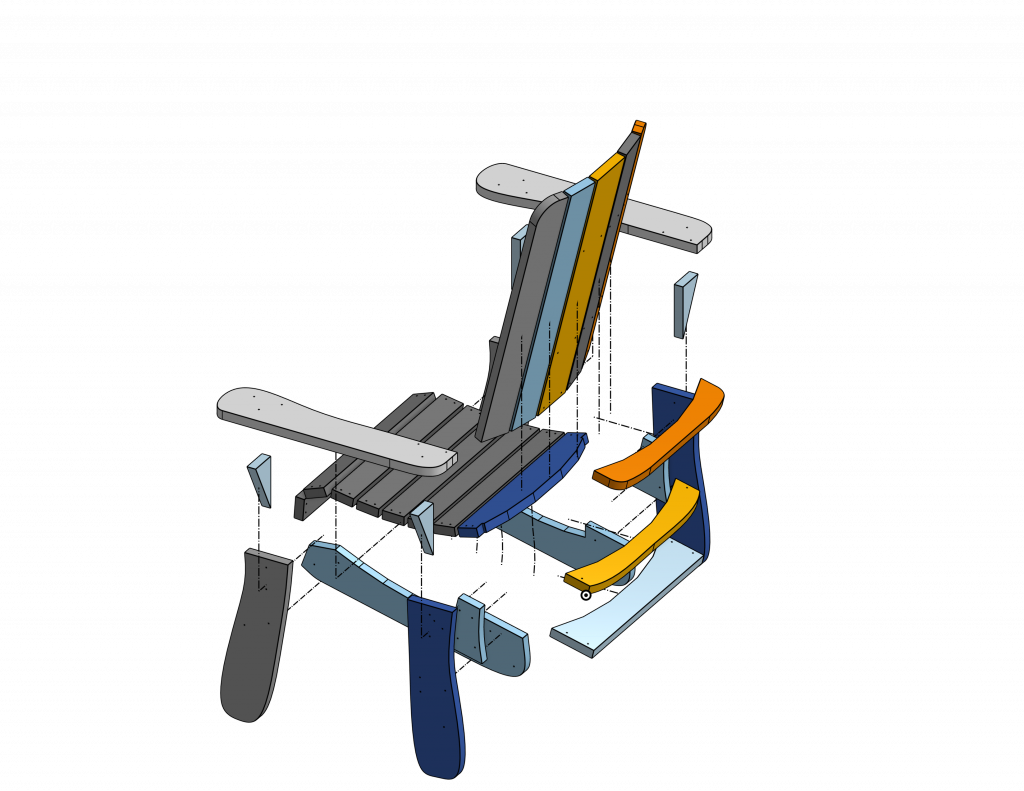
All of the parts are designed to fit together with quality, #8-1.5″ wood screws. Holes are pre-drilled with the CNC, but you may need to drill additional holes into support parts such as the triangles and the back supports.
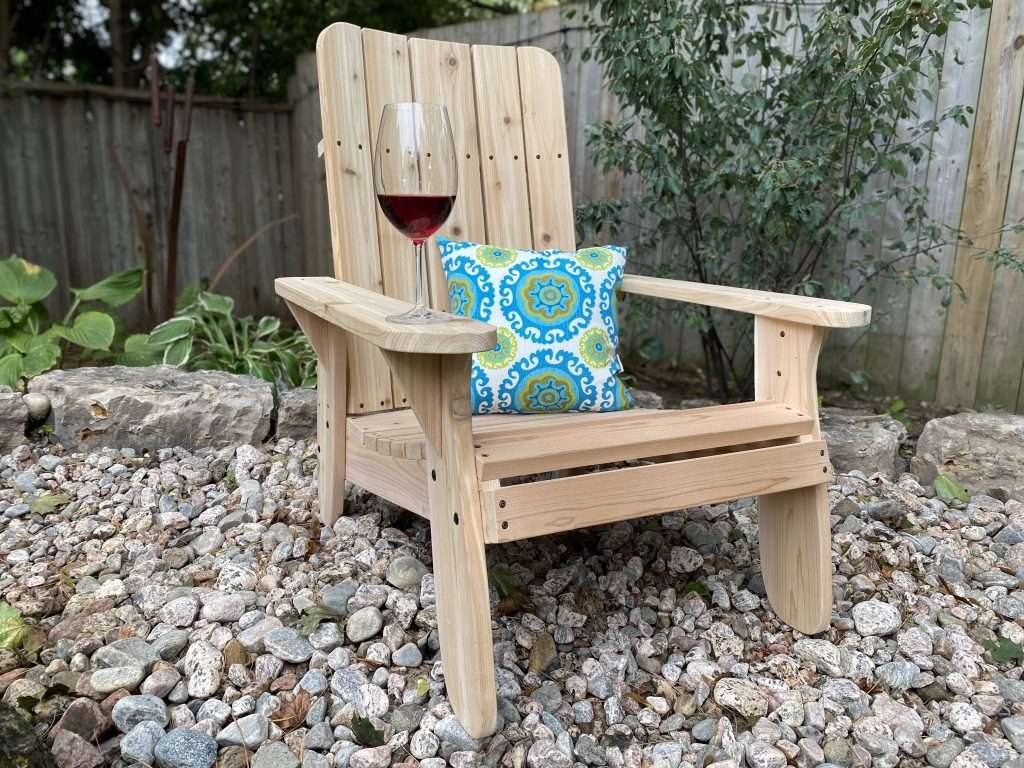