Hi everyone. We are now back from the holidays and full force into getting orders shipped out. Here are some news and updates for this month.
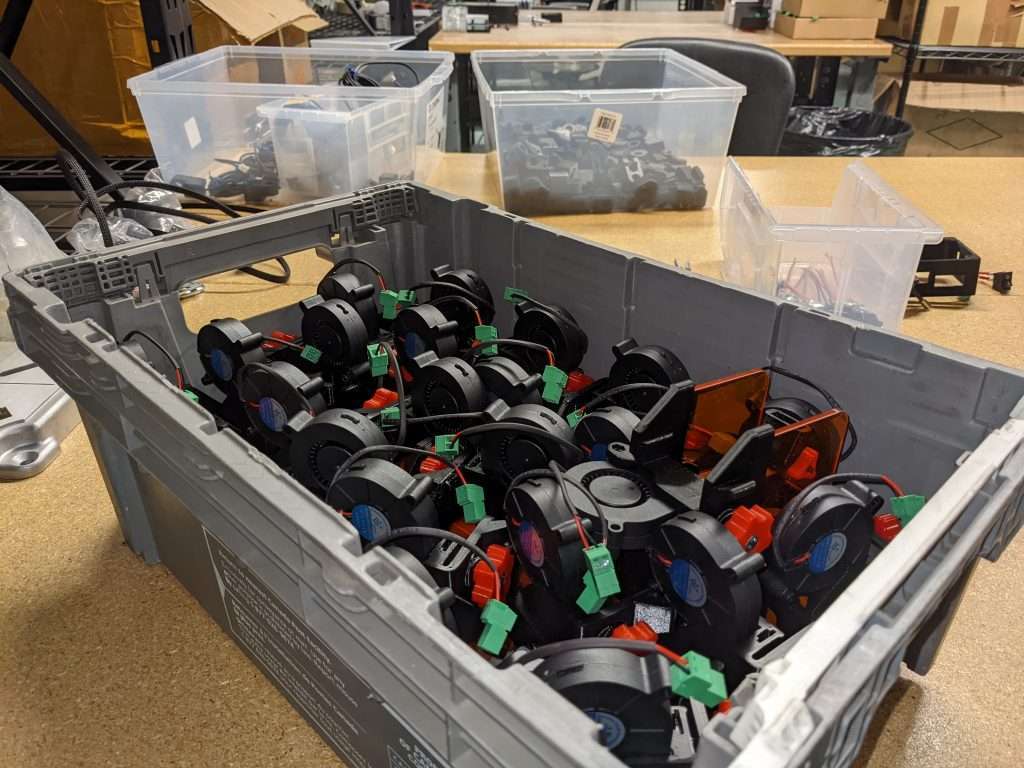
LongMill MK2 is now open for pre-order
LongMill MK2s are now open for preorder. For complete info about the updated version of the LongMill, please see the update.
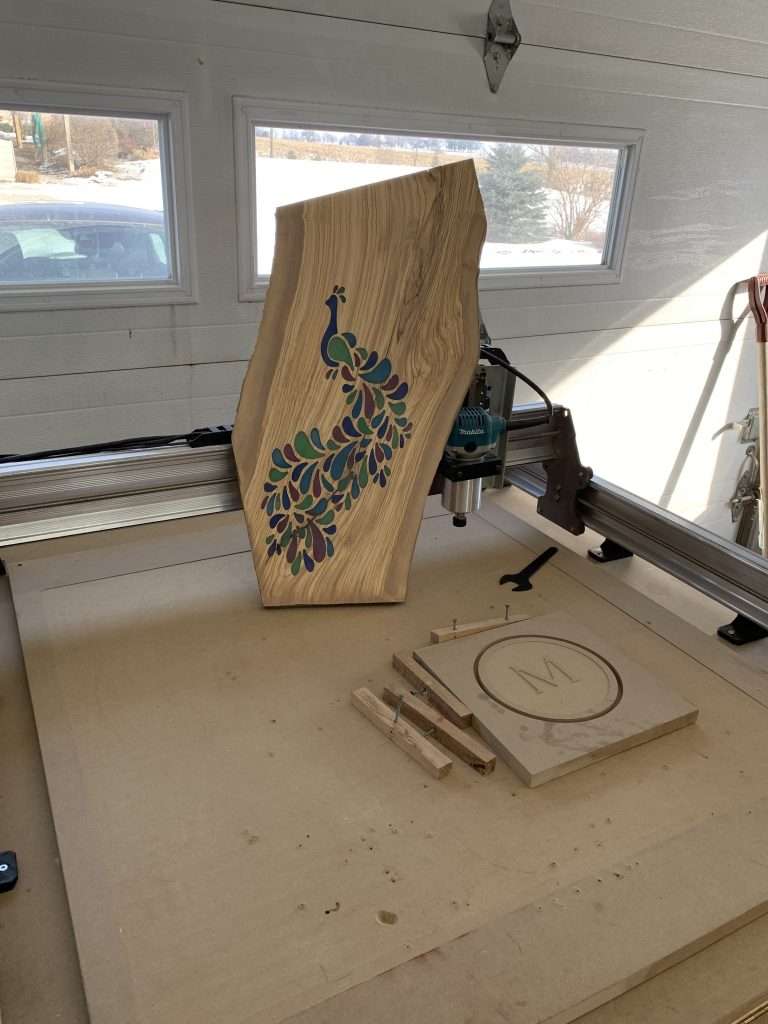
Pending LongMill orders
If you placed an order for the original version of the LongMill and you’re in the queue here, we are working on packing and shipping your order. We have been delayed in shipping the remaining LongMill orders as the couplers which were estimated to arrive on December 30, 2021 have been delayed. Due to the delay, we have ordered a rush batch of couplers which are expected to arrive around Jan 12th, and shipping for LongMills will be temporarily halted until the couplers arrive.
We’ve sent customers who are expected to be affected by this delay emails over the holidays to let them know ahead of time. We are currently assessing estimated delivery times for the remaining orders and will provide customers with updates soon. We’ll be updating order statuses on our Forum and our new Order Status page.
Response times for customer service (emails, tickets, and phone calls)
We have been overwhelmed with emails, tickets, and phone calls from customers, especially as we get caught up with messages that have come in over the past week while our offices were closed. We are working hard to respond to all of our customers, however, it may take longer than usual to get back to everyone. Thank you for everyone’s patience.
COVID situation
COVID 19 cases in the Waterloo region have seen a large increase in recent weeks. We recently had one of our employees coming back from vacation test positive for COVID 19. Fortunately, they were not exposed to everyone else at the shop as they tested positive before they came back to work, but it feels that a potential outbreak in our workplace becomes more and more likely as the pandemic becomes more severe.
To help keep our employees safe, we are pushing more of our staff to work from home. We are continuing to work to help set more of our staff to work from home and reduce the number of people at our office.
We continue to ask folks that are picking up orders from our office to stay inside their vehicles for pick-ups instead of attempting to enter our building without permission.
Lead times for LongMills and LaserBeams
We continue to wait for parts to arrive for the LongMill, LongMill MK2, and LaserBeam kits and ship products out as materials come in and get processed. We’ve created a new system for people to see the status of their order and see where they are in line for shipping.
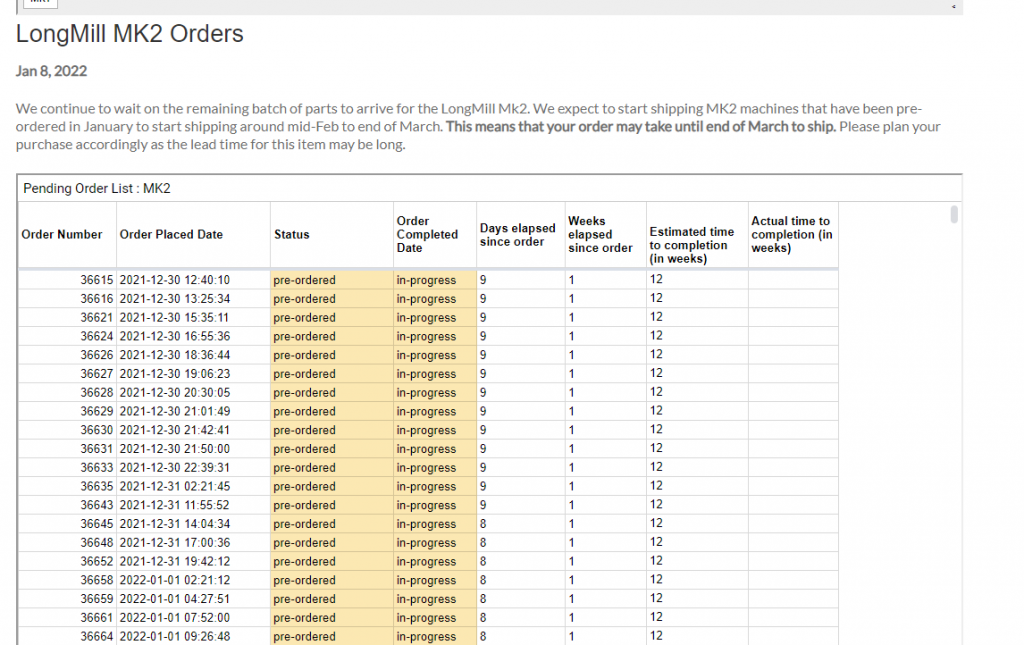
Doing customer service when lead times are long for your products is particularly challenging for a number of reasons, including:
- Folks are antsy about when they are going to get their machine, especially since they spent hundreds if not thousands of dollars on something from a random company on the internet (us)
- It’s hard to keep track of when the order was placed and when it’s supposed to show up, as well as remember the estimated delivery time that was promised
- There’s a lot of anticipation and excitement built up, which quickly turns into frustration when there are delays
- Folks want to get their things to line up with their personal lives, such as with holidays and vacation time
We made some mistakes in terms of communication and setting expectations with our customers on when their machines would get delivered. For example, we said that we could ship a certain number of machines per day, so customers were expecting us to be shipping that number every day. However, because the number we can ship is limited to other factors, such as parts availability and the number of machines that the couriers can take that day, we were not clear on the fact that the number that we said we could ship was not always the number that we actually shipped. Some of our customers were calculating the number of days they would be waiting to get their machine based on the best-case scenario.
More realistically, customers should be planning their delivery based on the number of weeks that we advertised on our order page at the time the order was placed. Typically, the lead time will be stated as a range of weeks, such as 4-6 weeks.
The second mistake was how I sent the email out about the delay on the couplers. As some folks may know, the shipment of couplers that were slated to arrive on Dec 30, 2021, but was delayed until the middle of January. I emailed customers that this may affect the delivery time of their order. This email was only sent out to a small handful of customers who would potentially see that their orders would ship outside of the initial lead time that was promised, however, customers who the delay would not be affected also were upset that delays were happening, even though it would not affect the delivery time of their order as it is scheduled to ship later.
Our team is working to find new ways to improve transparency and communication with customers, but in the meantime, we’ve created a simple auto-updating list for new orders.
Our goal with this system is:
- Customers can see what the status of their order is at any time, reducing the need to contact us directly about the order
- They can see what the lead time was and how much time had elapsed, providing clarity on what delivery time was promised and if we are meeting them
Creating this system was actually a bit eye-opening as well. Given how much pressure we were putting on ourselves to ship quickly and manage customers with high expectations, we were feeling that we were always missing shipping deadlines. Now that we can visually see how much time had passed, it appears that we’ve been shipping almost all of our LongMills within our estimated times.