Hey everyone, please meet Andy McTaggart, one of our beta testers for the LongMill MK2 30×30.
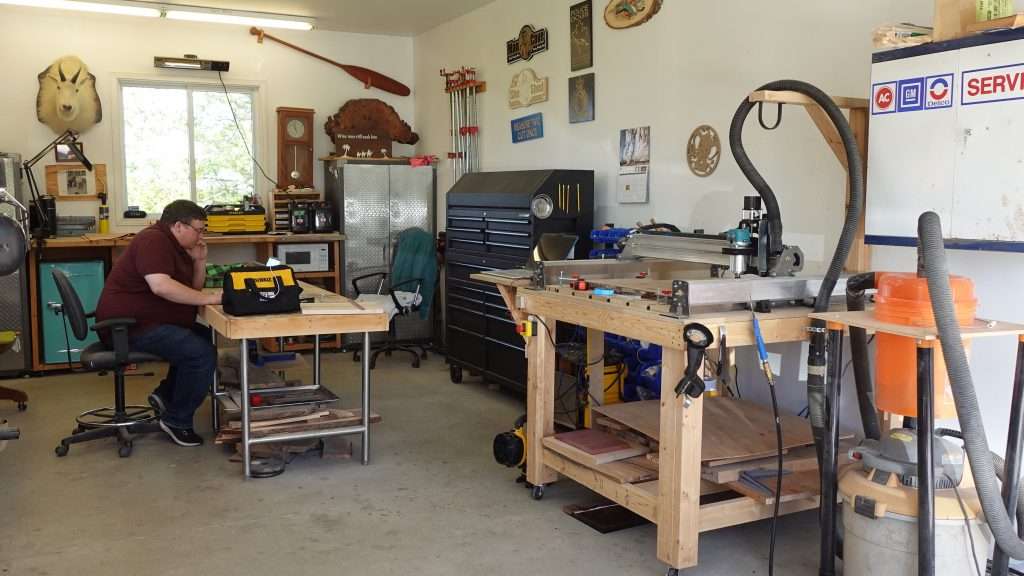
About the beta testing program
Just as a quick intro about the beta testing program, at the end of last year, we recruited three different people of different backgrounds and skill levels in our area to test the LongMill MK2. At this point, we were at the final stages of our development for the MK2 and were looking to iron out the rest of the kinks to finalize the production of a few of the parts. All beta testers paid for their machines, albeit with a small discount. Each beta tester volunteered their time and space to observe and interview them at each step of the process as well as testing prototype and production parts as they were made to update their machines.
Working with Andy
One of the funny things about Andy having the LongMill was that he had done quite a lot of projects, but his family had been taking so many of them he only had a few projects on hand to show. I guess it’s sort of a good thing because it means that over the last few months of owning the machine, he’d been able to get up to that level of caliber. It was at least great to see some of the photos of the projects, however!
I thought it was also funny that although we gave Andy all of the new production parts, he’d just ended up using the old prototype parts, minus the XZ gantry which has the holes for the new dust shoe. This includes the 3D printed Z-axis motor mount which we switched to aluminum. Even still, the machine was chugging along totally fine.
I guess this speaks to some extent on how far we’ve come with mechanical design. Previously on the LongMill MK1, we made a lot of changes to the design of the MK1 before finalizing it for production. For example, the MK1 beta testers, instead of getting drag chains, got foam pipe insulation for wiring management, since haven’t even figured out how to use drag chains properly. In comparison, there were only minor changes from prototype to production in the MK2 machines.
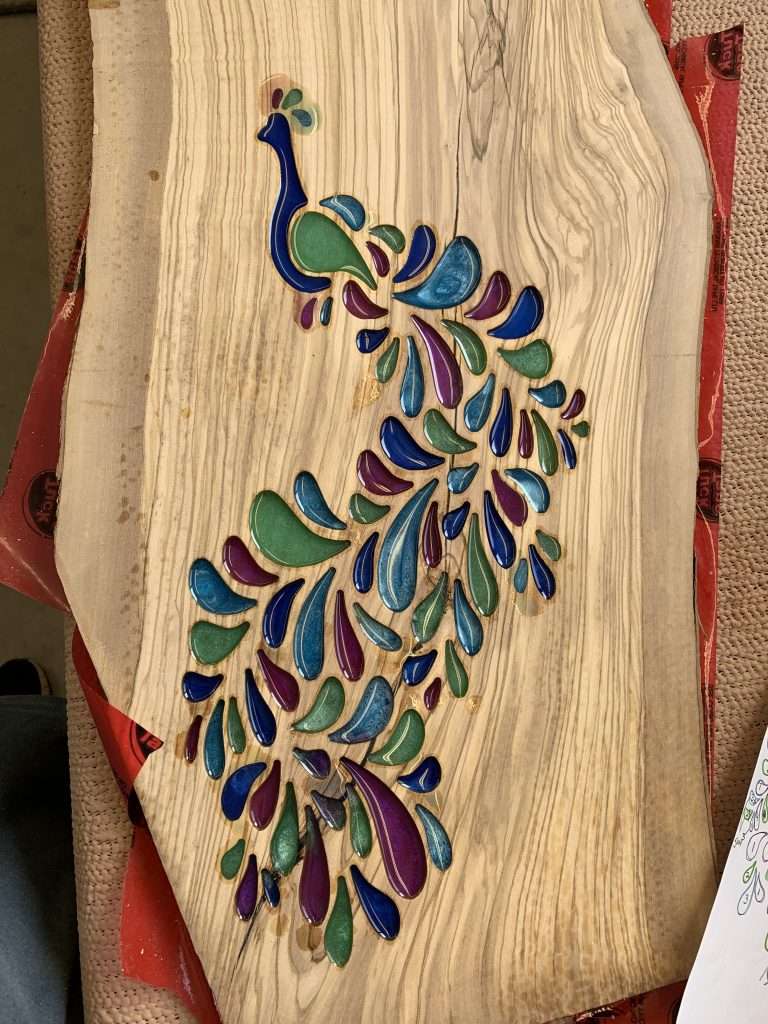
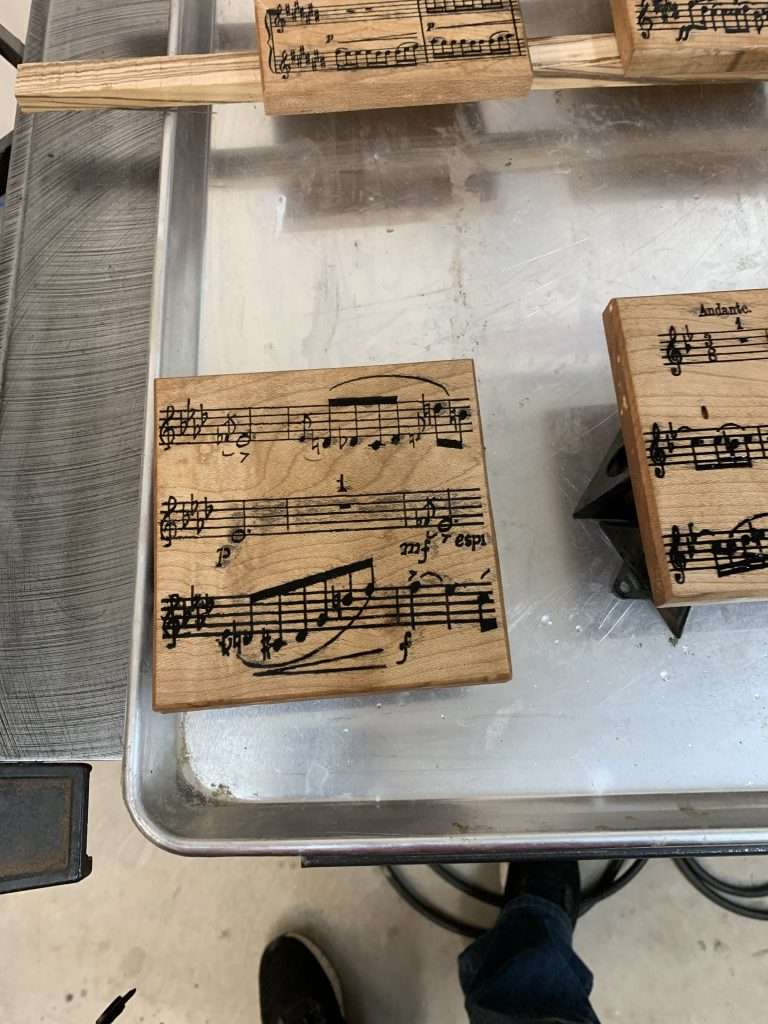
Is it time for us to support spindles?
The one really big thing that I noticed from his demo project was that when using the ball end router bit for the tray, his Makita would noticeably slow down. We had the router speed set to full RPMs and while the LongMill itself chugged along like a tank, I saw the router be the bottleneck.
Because most of the projects I’ve been doing myself have been mostly with 1/4″ and 1/8″ bits, I hadn’t really run into the Makita router as a bottleneck, but in some types of projects, such as surfacing and using router bits, it seems more apparent that the LongMill MK2’s rigidity is more than enough to handle more power.
Originally we’ve recommended our users to stay away from spindles, and we had a few reasons for that.
First is from necessity, as we didn’t really see much benefit from using a spindle when the Makita was powerful enough, and we felt it was not worth spending an extra few hundred dollars on it.
The second was complexity. Given that most of our customers are beginners with little to no electrical experience, and given that from our experience, programming and wiring VFDs can not only be complicated but also dangerous, we didn’t want customers to jump into it without some CNC experience first. It’s also quite difficult to purchase the right spindle and VFD. As someone who’s ordered, programmed, and tested a couple of different low-cost spindles, oftentimes I’ve found that there is basically no support and the wiring inside is many times not made to a safe specification. Also, I’ve had a few VFDs also break and stop working as well, and of course, it’s difficult to get support on those as well. I’ve yet to try some name-brand VFDs, but given that they can be a lot more expensive, I feel that they may be out of budget for most of our customers.
And lastly, because the mechanical structure was one of the limiting factors of the machine, the machine itself would not be able to take advantage of the spindle’s potential.
In truth, we have actually wired and tested spindles on the LongMill MK1 and have overall been able to use them. I’ve found that although they are much bigger and chunkier than a regular Makita, they will run on stock settings.
Now with the updated, full metal Z-axis design, as well as the overall redesign of the rails, the mechanical structure of the machine is no longer the bottleneck in performance. I’ve started doing some testing on the machine to see how the machine would behave using a spindle. And also as part of the design process for the MK2, we made sure that there would be enough clearance for standard-size spindles as well.
Also, now that we have a bigger community of companies that cater to the CNC community, we’ve seen spindle kits come on the market that I feel are better set up for this type of application. The spindle kits are also coming from companies that have a better reputation for quality control and support, which makes me feel more comfortable in regards to people trying to use spindles for the first time.
Given that we have the AltMill in development, which will most certainly need a spindle, I think it is a good time for us to revisit supporting 3 phase spindles again. I think it will take a long time for us to find a high-quality source for spindles and VFDs and create the right documentation and resources to provide the right amount of support, but given general interest from the community, we feel that we’ll have a lot of interested people.
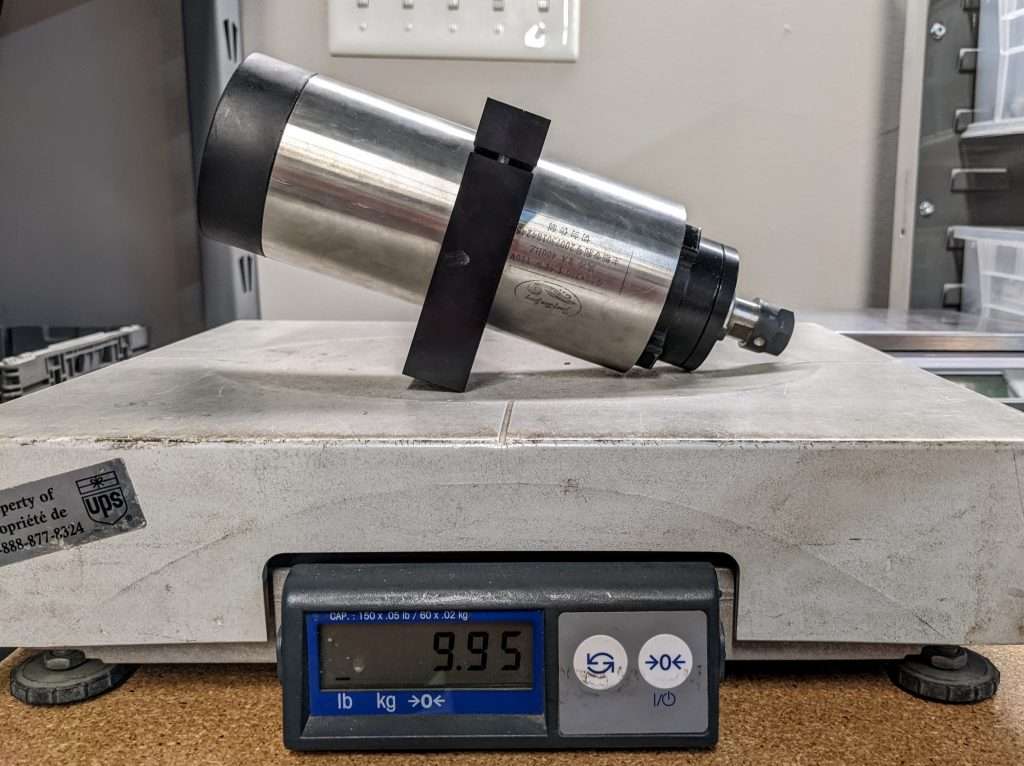
So just as a basic test, here is the LongMill hefting a 80mm spindle weighing about 10lbs for reference.
In this test, we run the spindle up and down for about 3 hours at 7000mm/min, which is a lot faster than the 3000mm/min default on most LongMills.